Yesterday we decided to use our leftover foam and make a hard top for the dodger on our boat! <Click here> Today we got up and going so we could hopefully get to the boat earlier than usual and get some fiberglass put on before the sun started beating down. Well… this is Florida and if the sun is up, it’s hot. The problem that we’re going to have is that we only have face cure epoxy because we lived in Washington where it’s cold. I had it set up spontaneously in Washington while working in the sunshine a few times so trying to use it here is going to be very difficult. We’re going to have to work FAST! 😮
We decided to run a strip of glass down the middle of the foam, avoiding the wire that we have it tied on with. I’m hoping this will strengthen it enough to be able to take it off of the boat and fiberglass the underside, but we will see. We did figure out how to use the boom and the sun shade to have half of the top be out of the sun, so that’s something!
Working together we were able to soak the fiberglass in foot wide sections and work our way down the sheet with Jason pouring and mixing more epoxy and me rolling. We got it done without any of the epoxy setting up too soon! Success! (I had a roller start smoking and bubbling up on me once.. seriously…)
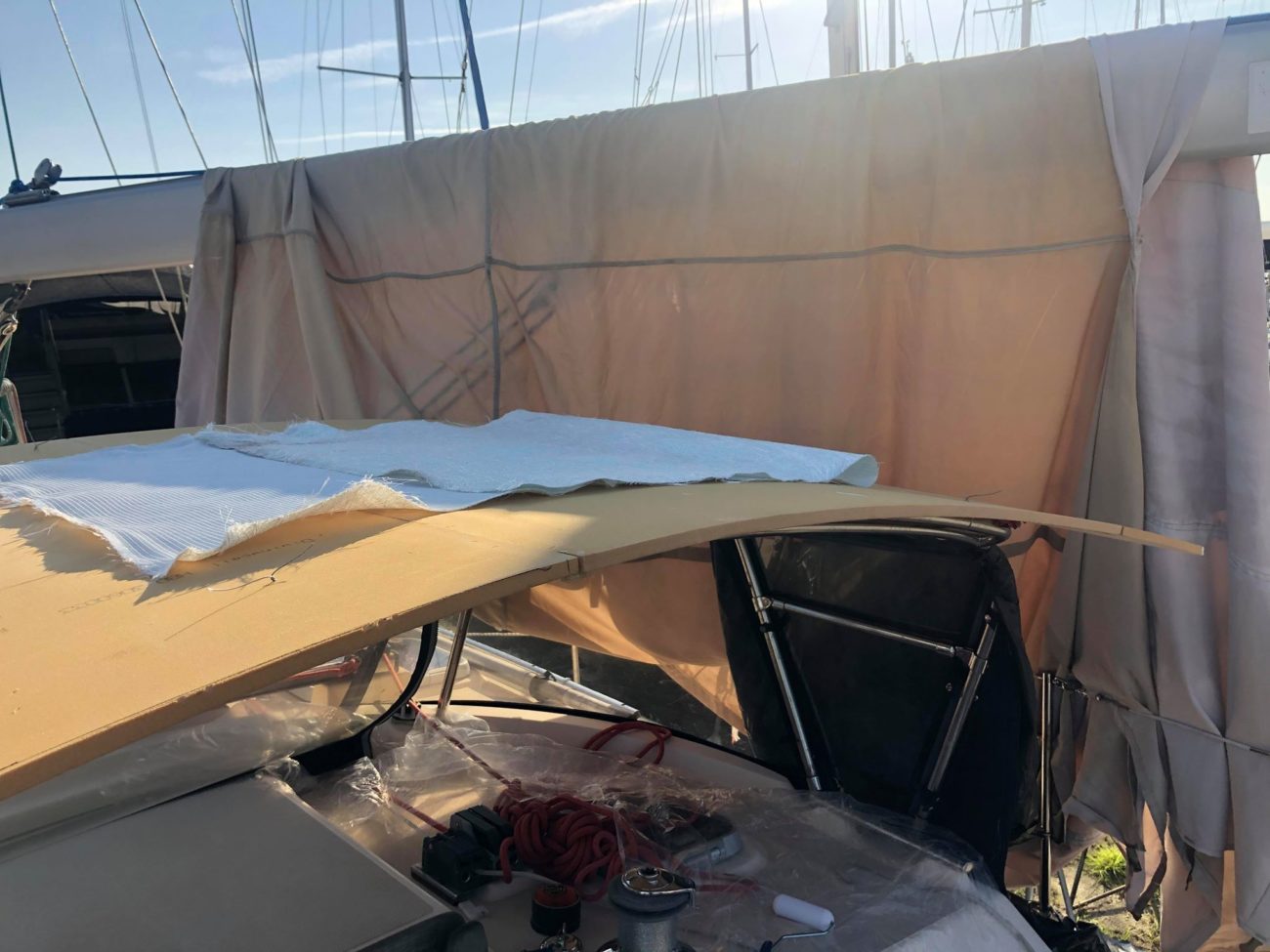

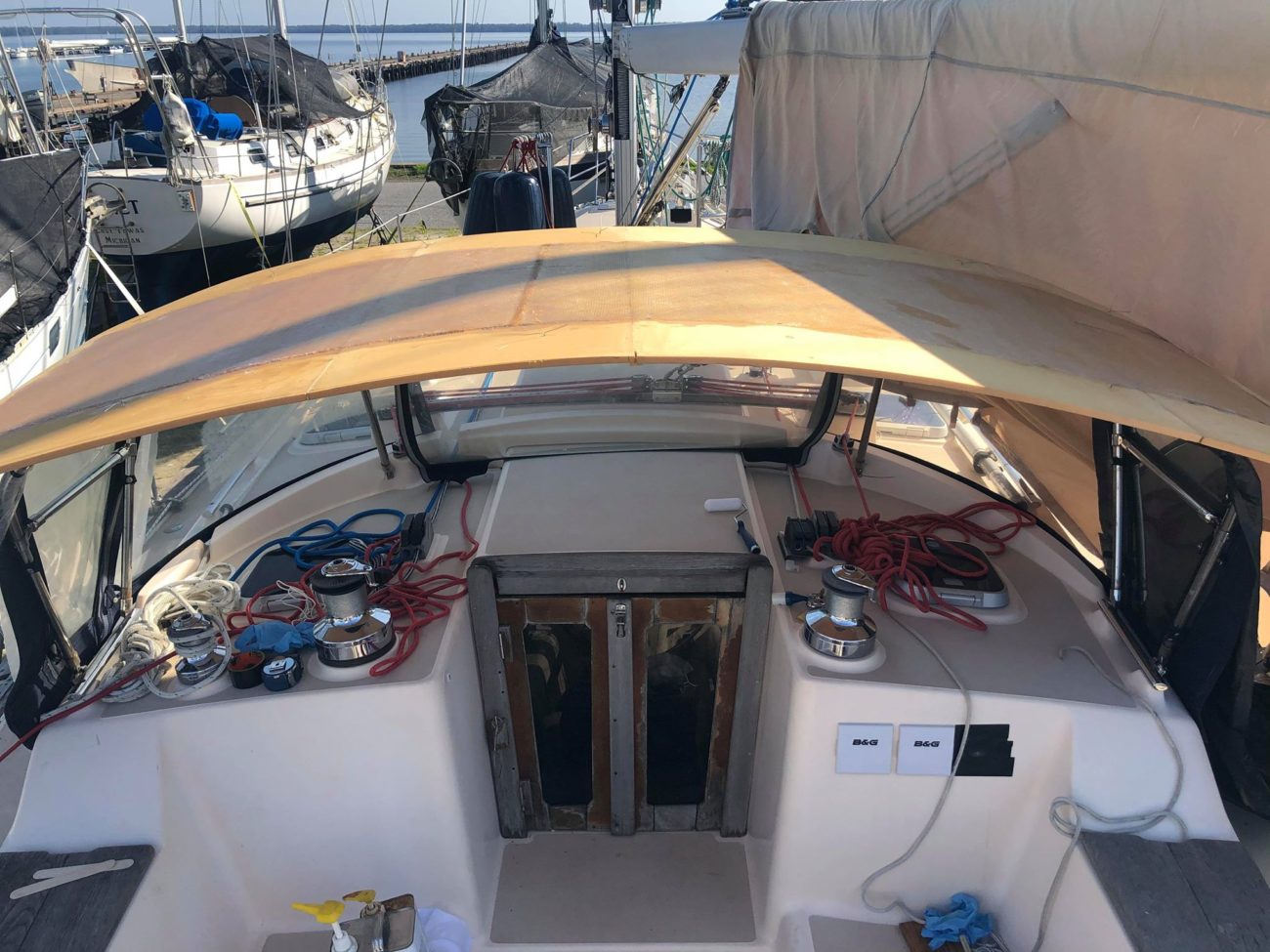
After we put the glass down, we took a break and did a few things inside the boat (in the AC!) After a few hours we went back out into the heat and glued on the rear corners of the lip and the “spoiler” on top. We’re going for style points now!
Hard to see it under the plastic, but I think it’ll look nice.
We took another mid-day break while it was too hot to comfortably work outside. When you have to question whether the sweat dripping off of your face is going to affect fiberglass lay up, it’s time to call it! 😉 After a few hours and some tasty dinner, we headed back out to finish up the perimeter and glue some more foam together!
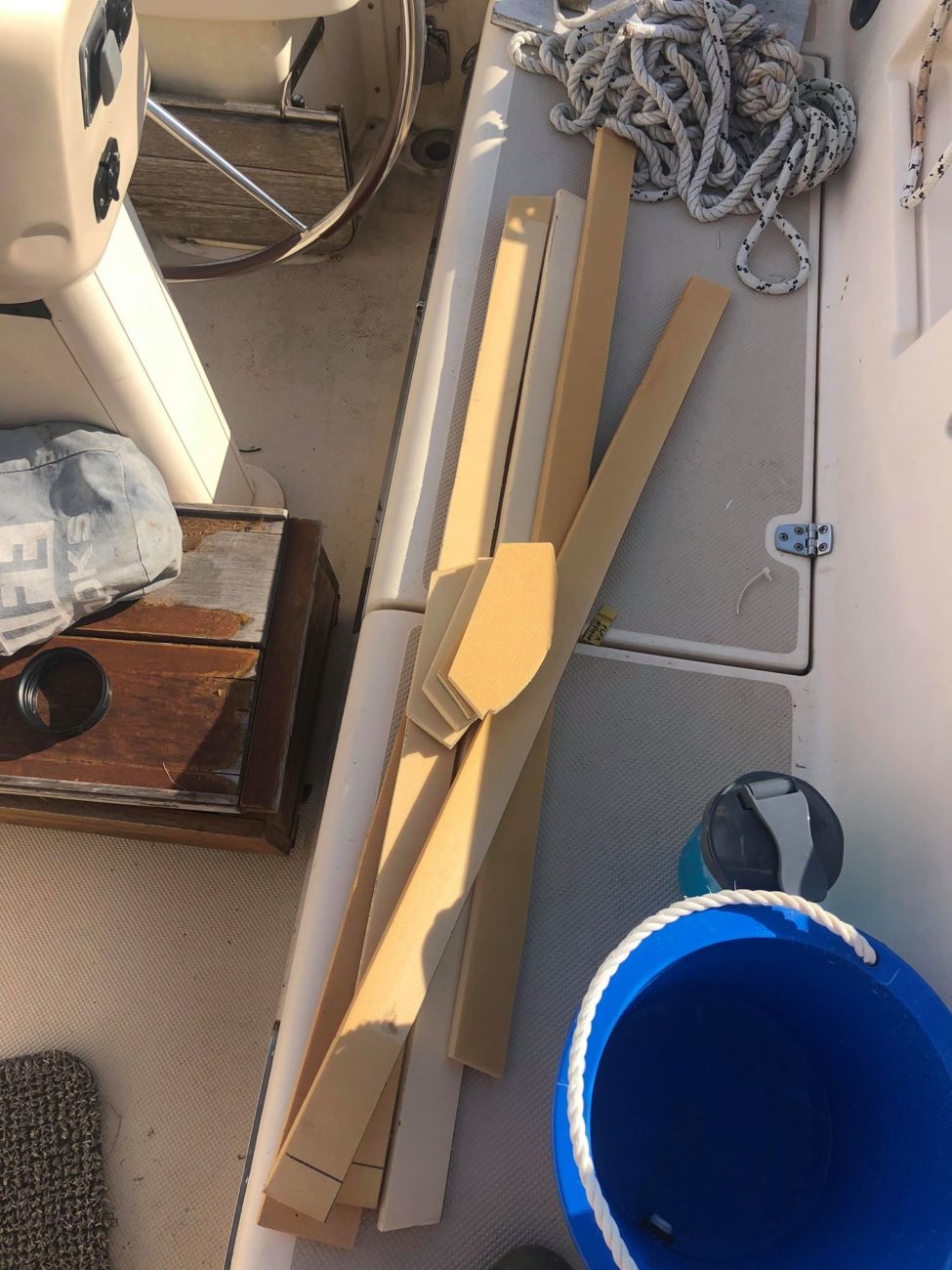

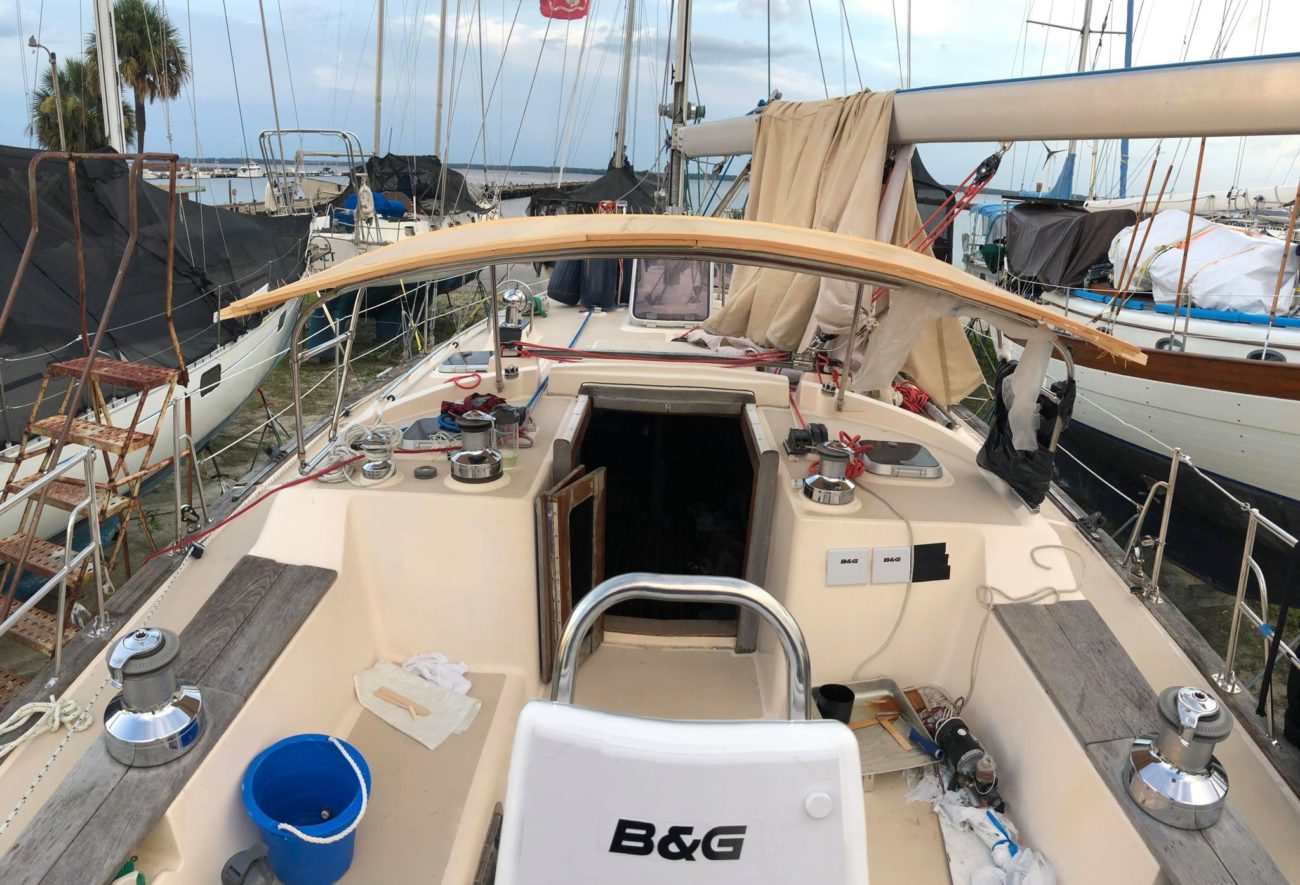
The lip on the back is on the top edge of the dodger while the sides and front will be below and will help the fiberglass look thicker, without actually having to add another inch of foam.
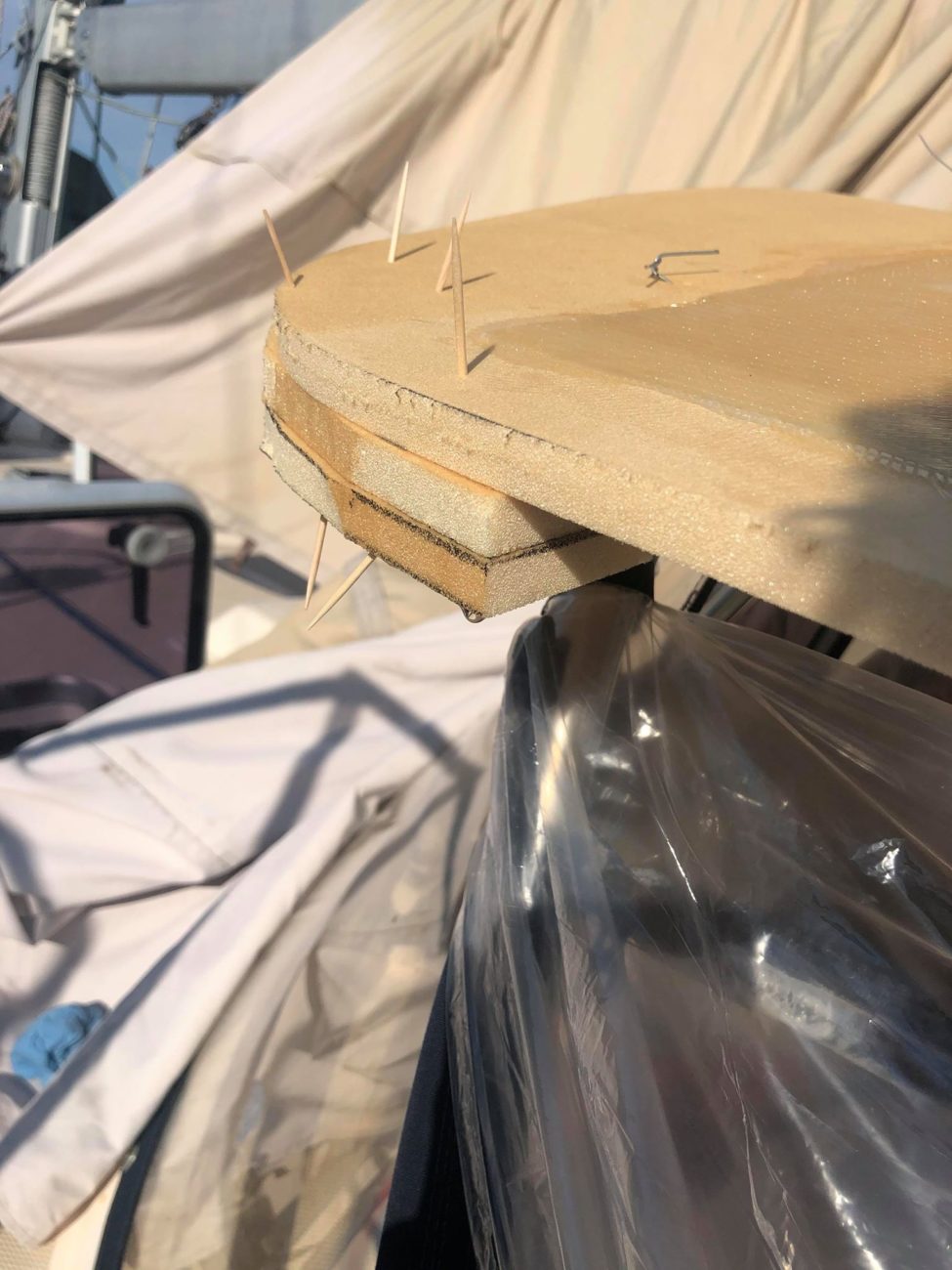
I’m going to try and sand the foam so that it’s a smooth transition from the bottom foam to the top foam. It should look really nice if I do it right! (no pressure…) The sides went on easily, as did both of the corner pieces since Jason had them cut and ready to go yesterday. We thought we were going to have to use the stupid pink house insulation foam for the front lip, but we found yet another Divinycell scrap in the boat that we could use to finish off the front!
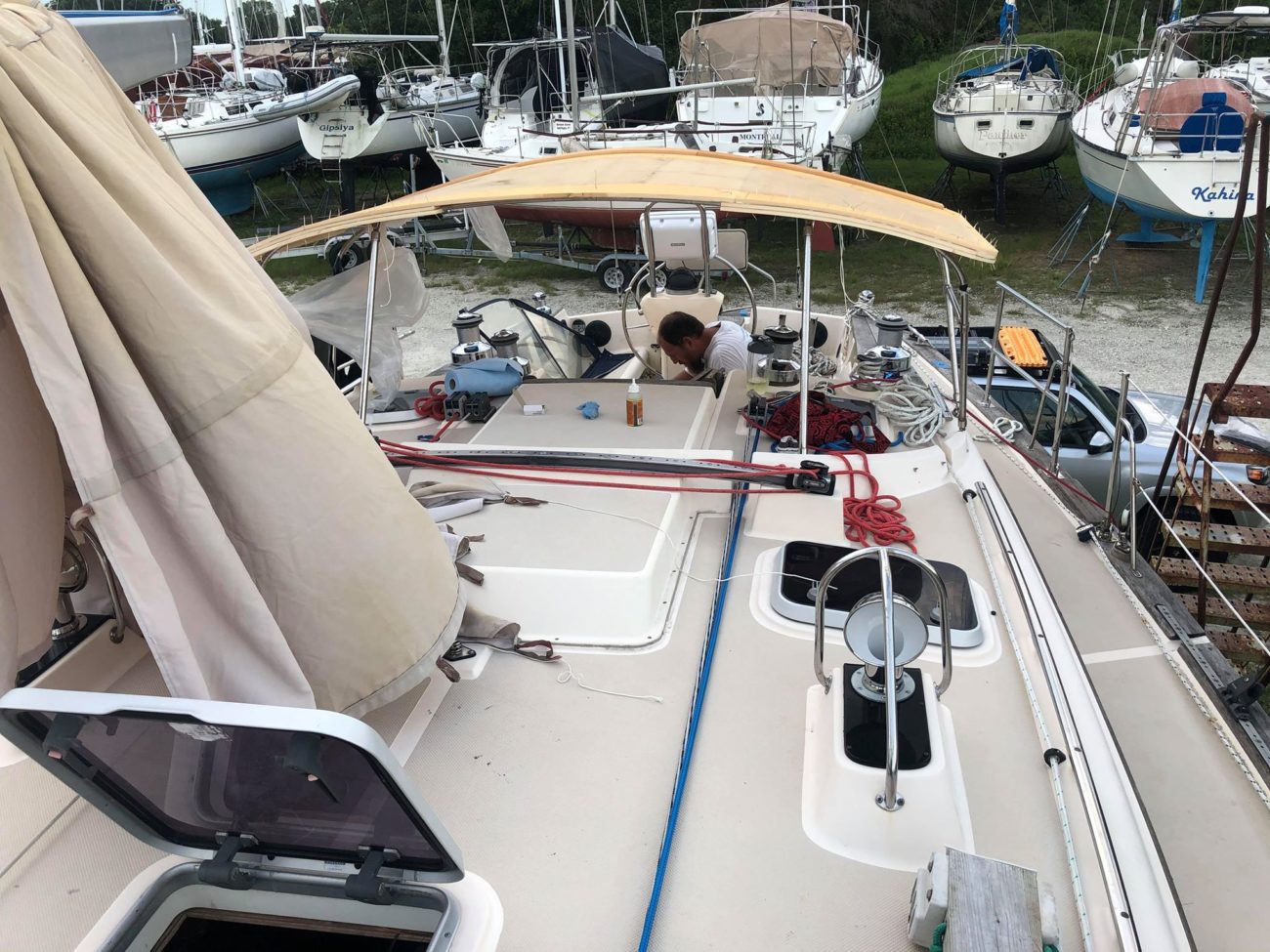
It took us a few hours to get the rest of the foam glued in place and held together with toothpicks. We used almost a box and a half of toothpicks so far and my fingers hurt from shoving them into the foam. It’s still easier than clamping everything in place and we don’t have the right clamps anyway. It looks a lot better with the lip on it!
Jason got on the neighbors boat to check on it and got some photos from other there! I think it’s looking nice! (even though it looks a little naked without the canvas in place!)
It’s starting to shape up pretty nicely! Tomorrow we get to cut off all of the toothpicks and start sanding it into the shape that we want! Not too shabby for a random weekend project!