Today we cut off all of the hundreds of toothpicks that we shoved into the foam to hold it in place and started the hot and tedious task of sanding and shaping the foam. (the toothpicks would have kept seagulls off of the hardtop, but it wasn’t meant to be!) It was a hot day again and until we get this hardtop done, we don’t actually have any shade! There’s some motivation! After a few hours of standing in the sun we were covered in foam dust and super sweaty but the edges of the top were lovingly shaped to the right angle and all of the edges artistically rounded off.
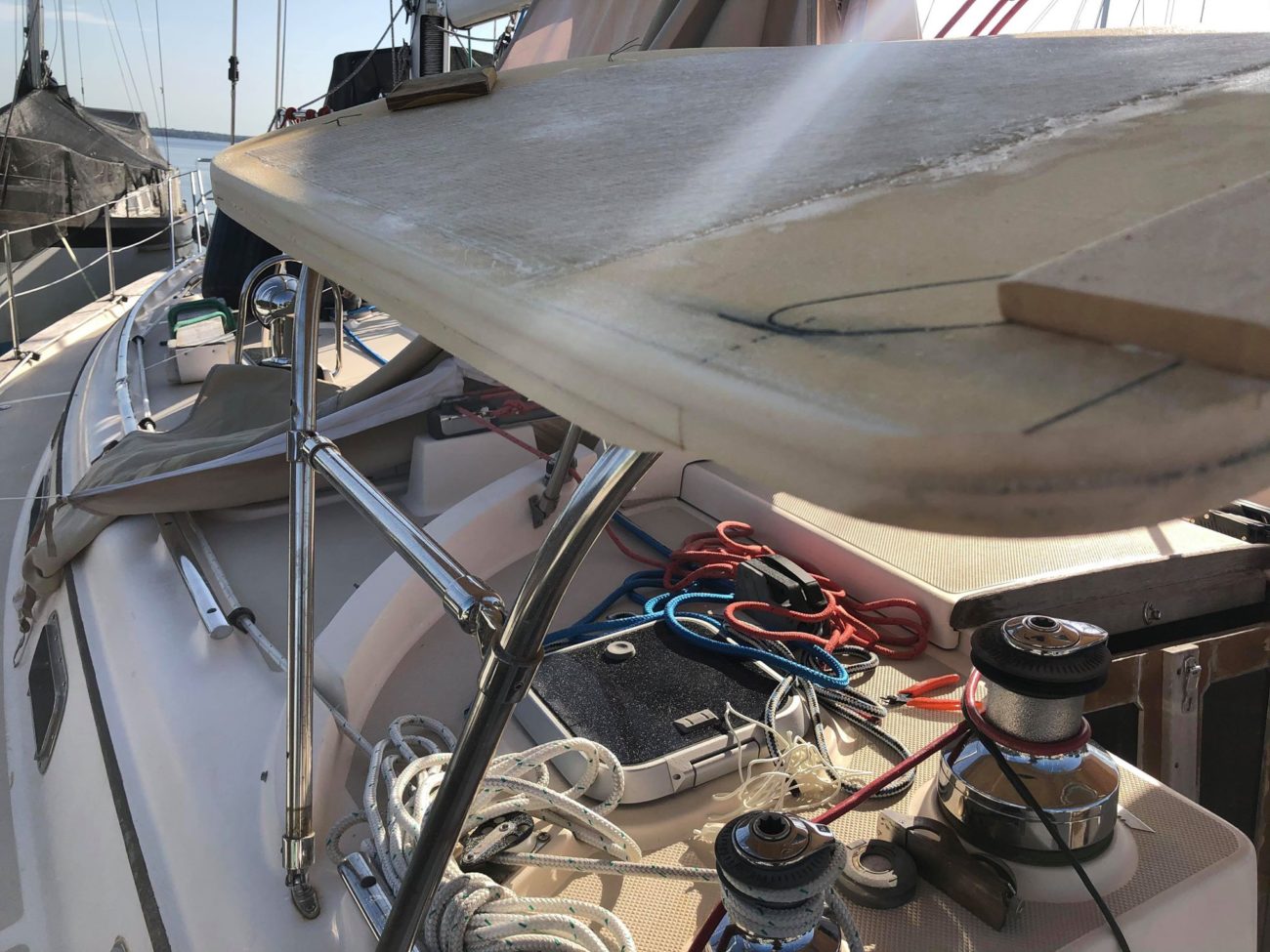
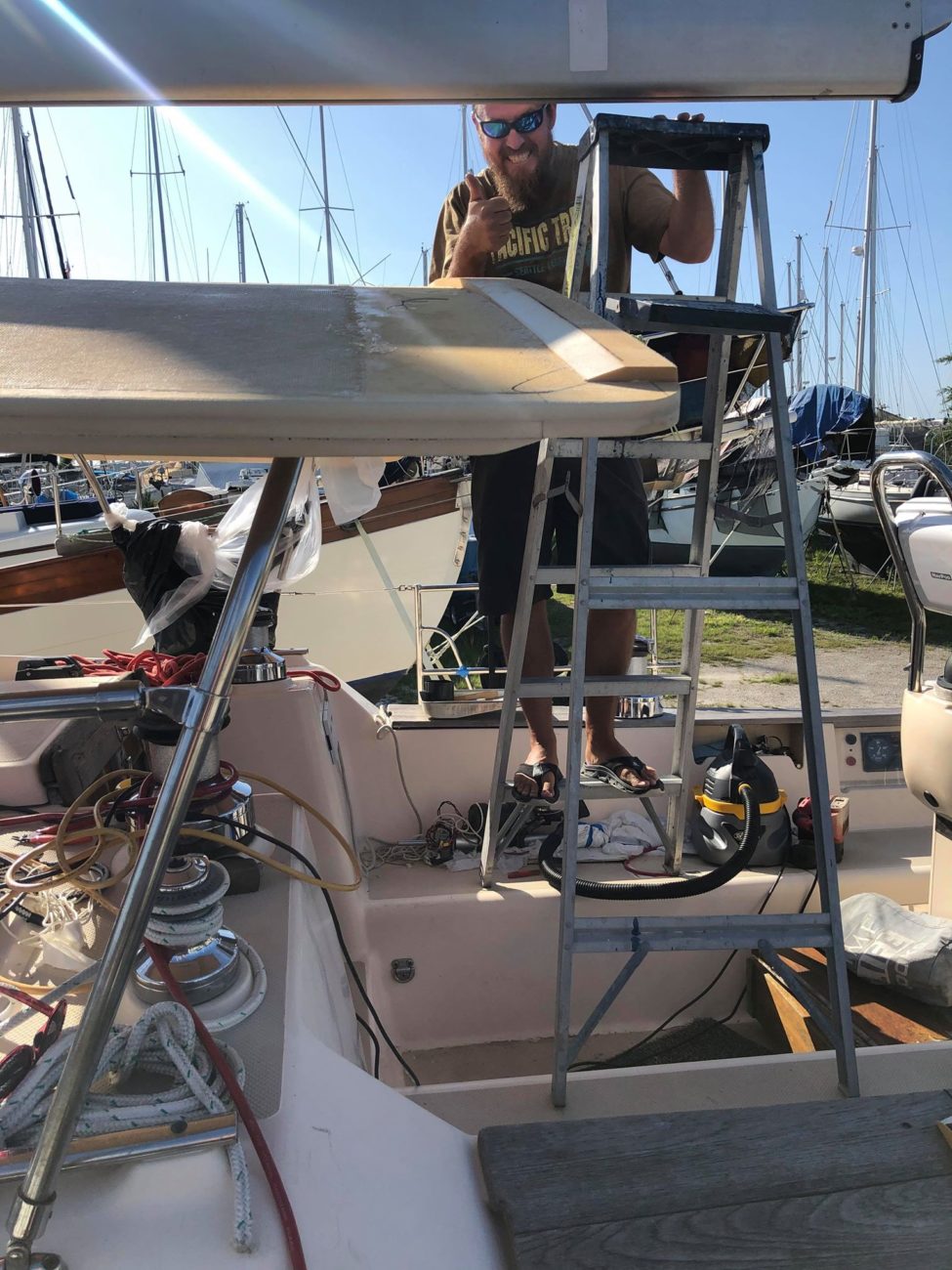
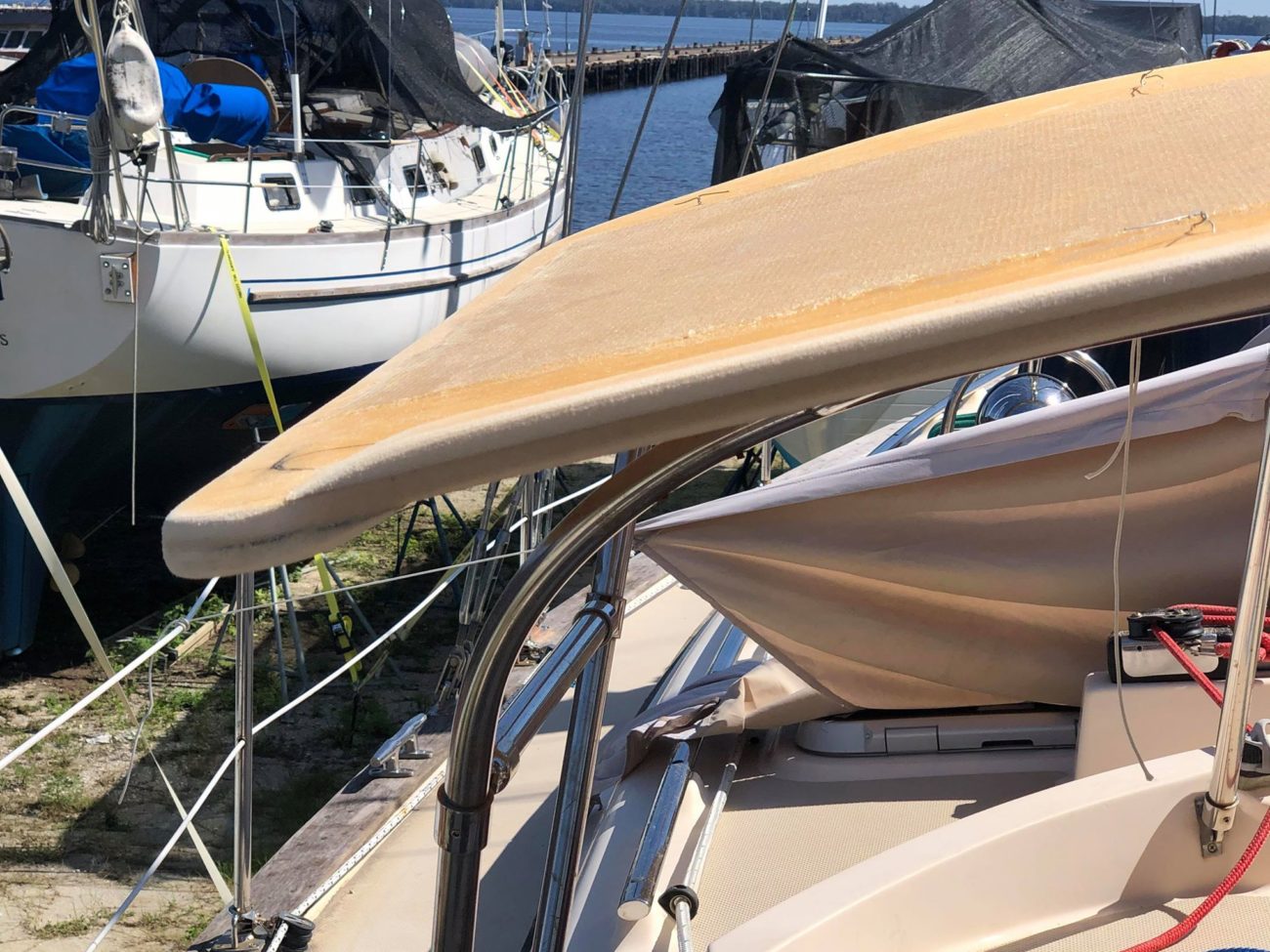
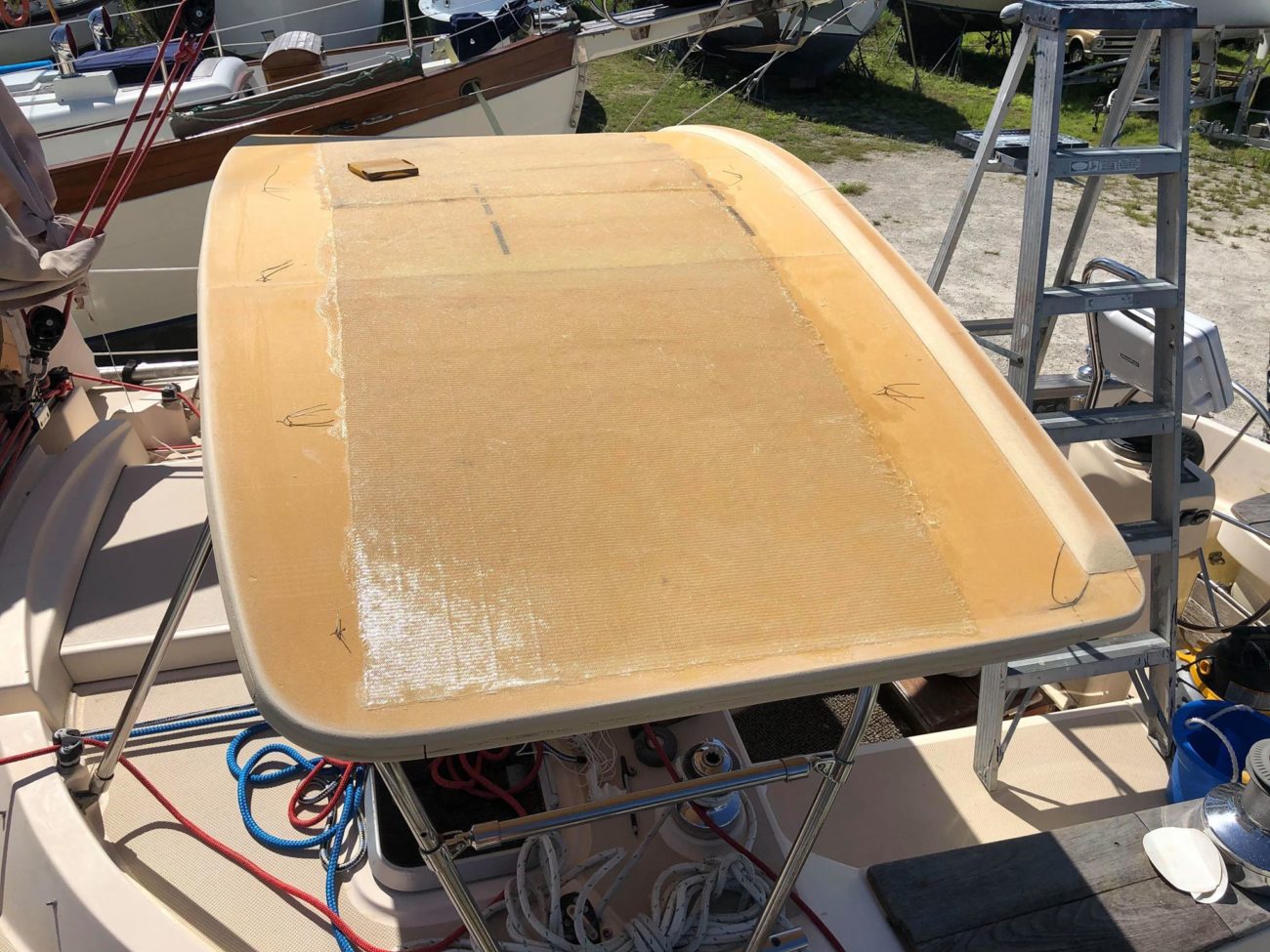
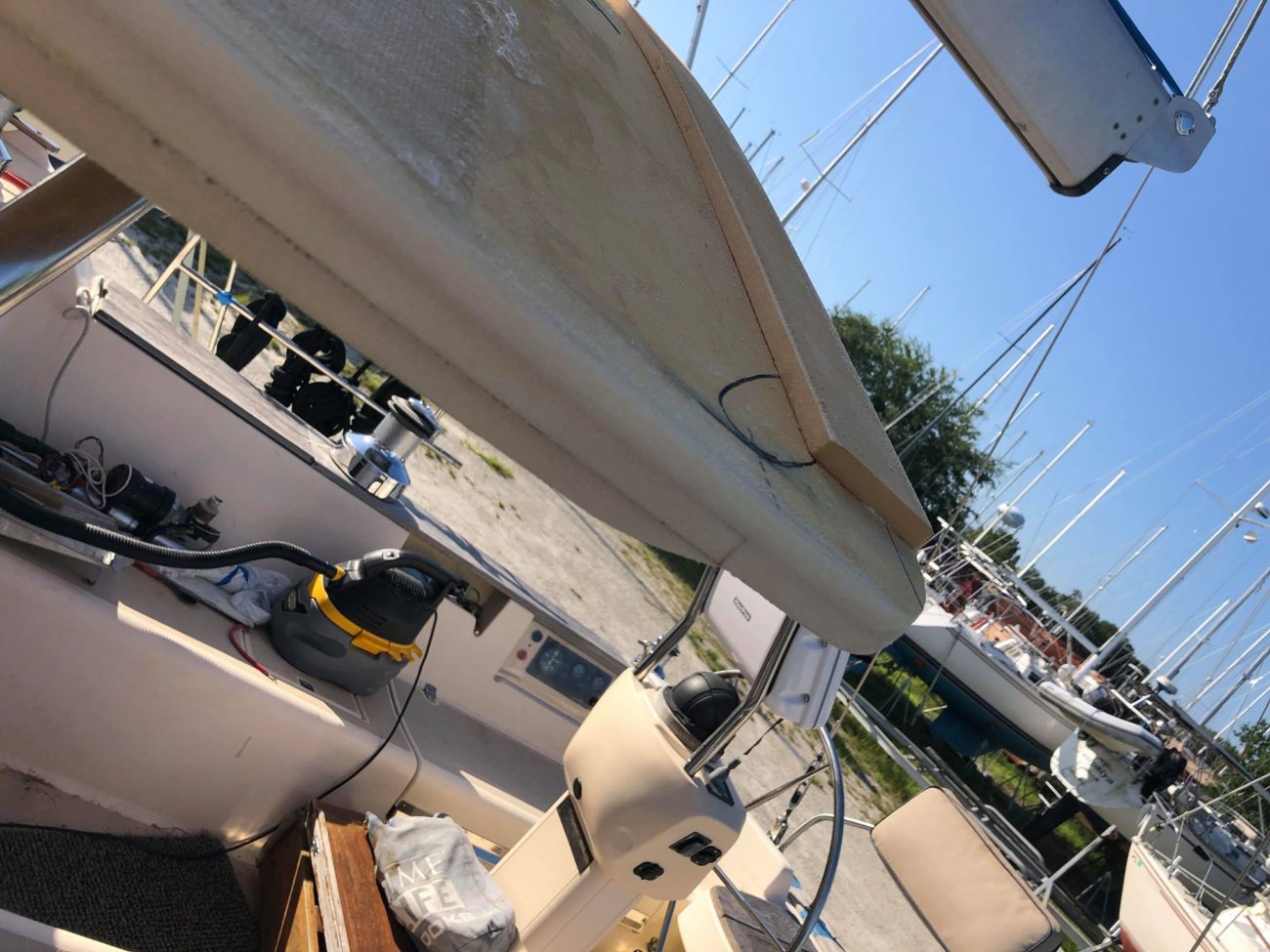
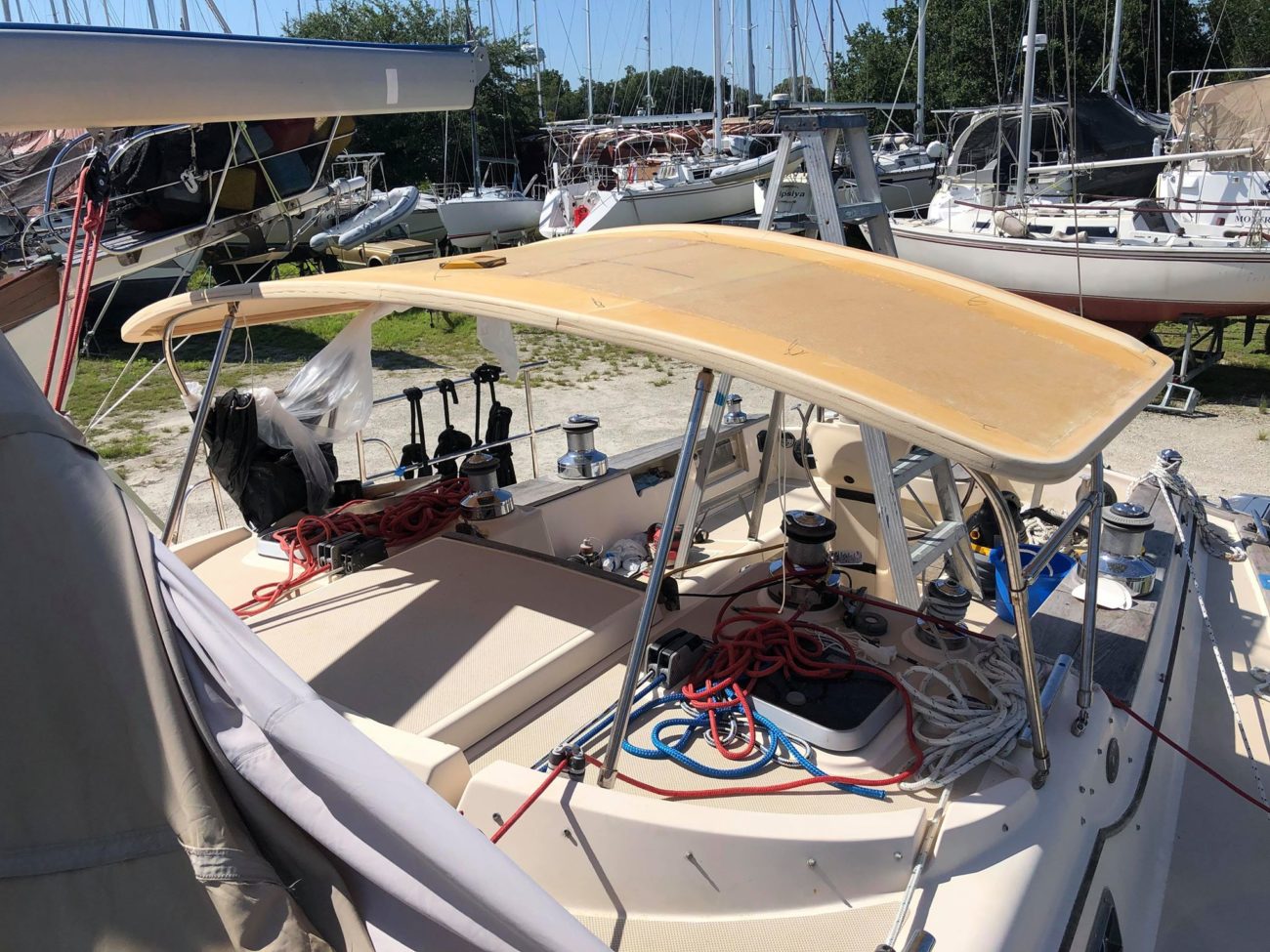
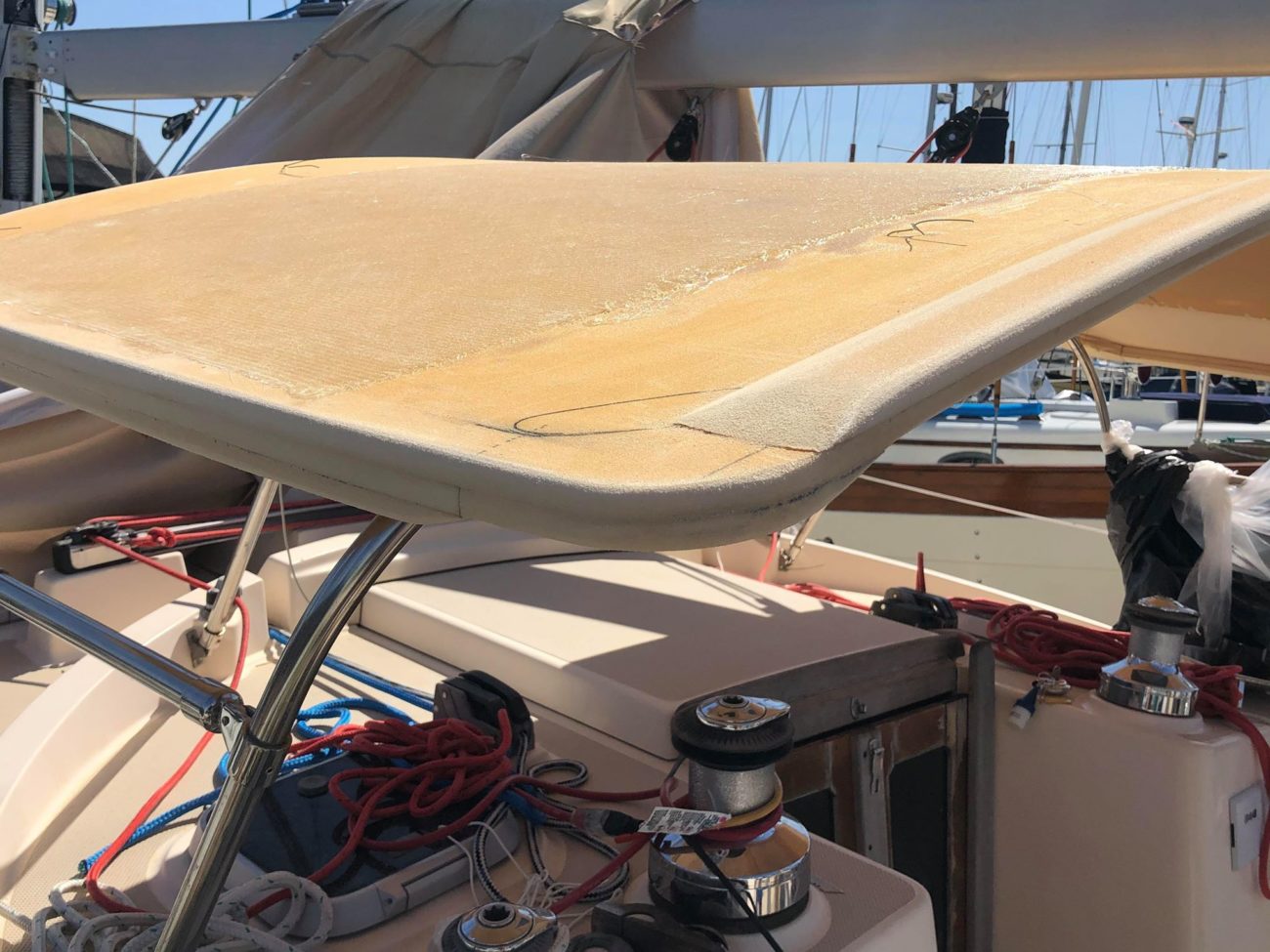
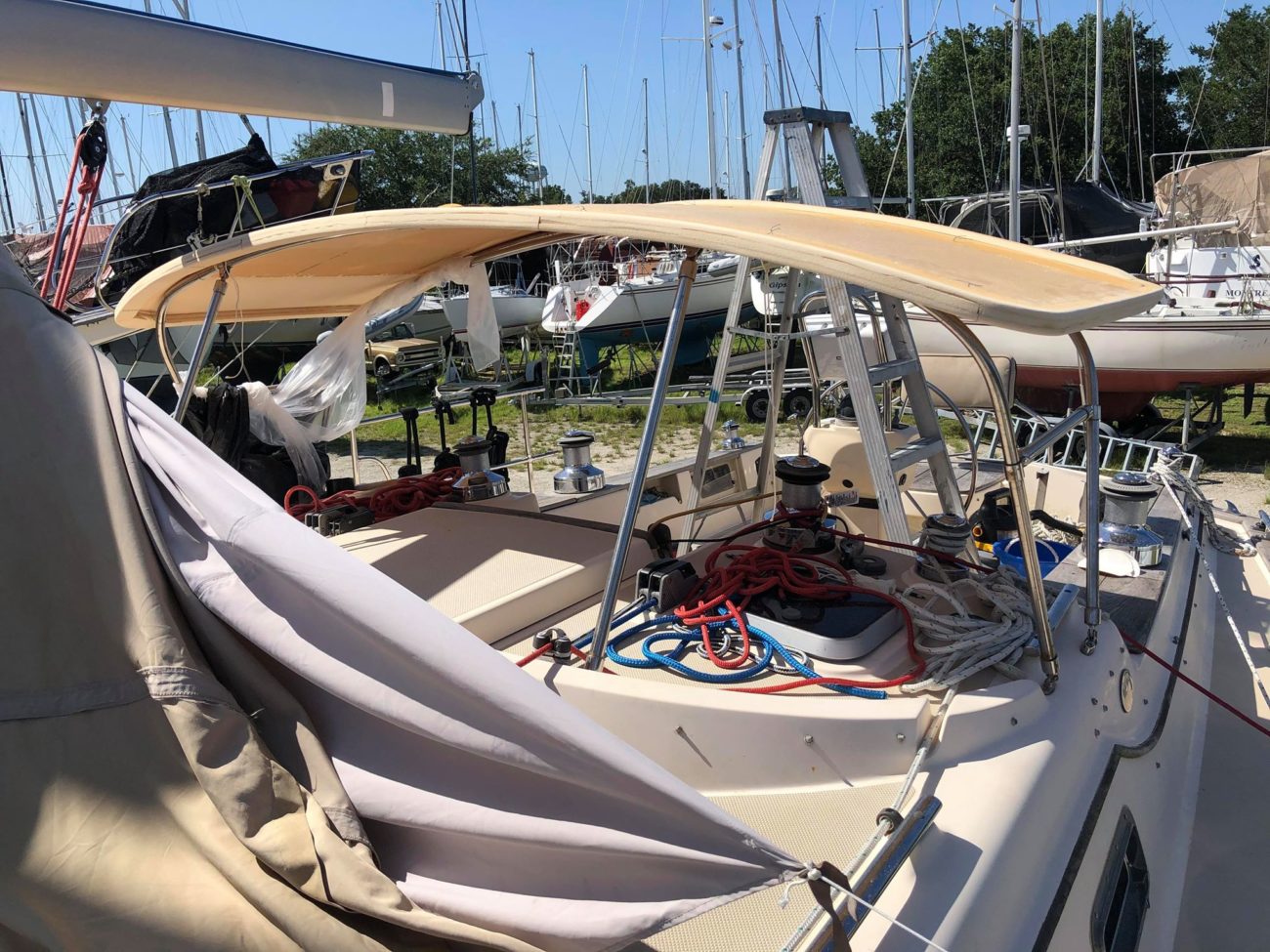
The foam is pretty easy to sand with a sanding block and 120 grit, so we made pretty quick work of it, except that there was a lot of area to cover so it still took all morning. Rounding off the edges really makes it look a lot nicer and more like a real thing. The lip made a big difference in giving it some “heft”. She’s a big boat and a little 1/2″ piece of foam wasn’t going to cut it! I’m also really liking the spoiler in the back, especially the transition to it. I think it’s little things like that that really make a difference in the final product. One other benefit to using foam instead of fabric is that the foam actually insulates very well. It’s noticeably cooler underneath it than before! I’ve even seen people install opening windows in their hard dodgers, so that might be an addition for later!
Hopefully tonight’s killer thunderstorm doesn’t rip it off of the boat (it’s still held on with just safety wire..) and we can do some more fiberglass tomorrow. We even have a new container of slow cure epoxy so hopefully every fiberglass experience isn’t steeped in pure panic at getting everything done before it hardens in the bucket!